摘要: 針對當前飛機制造企業(yè)信息系統(tǒng)眾多、質量信息數(shù)據(jù)來源不一致、對貫穿飛機研制全生命周期的產(chǎn)品設計制造過程數(shù)據(jù)及企業(yè)資源數(shù)據(jù)缺乏相應的數(shù)據(jù)治理與數(shù)據(jù)質量控制等問題,,通過分析公司質量管理現(xiàn)狀,,構建基于大數(shù)據(jù)的質量管控體系,,挖掘關鍵質量信息,,建立QBOM目錄結構的單機質量檔案,實現(xiàn)產(chǎn)品質量管控模式從事后被動檢驗轉變?yōu)槭虑爸鲃宇A防,,從而提高產(chǎn)品質量及成品率,。
關鍵詞:大數(shù)據(jù)、質量管控,、QBOM,、異地協(xié)同RFV、數(shù)據(jù)挖掘
1 引言
飛機制造是一個復雜的過程,,質量可追溯性要求高[1],。目前成飛集團的質量管理處于質量統(tǒng)計階段,百分之百全檢的檢驗方式有效地保證了產(chǎn)品的質量及可靠性,然而對質量問題進行診斷,、報警與維護的功能并沒有充分發(fā)揮,,如何更加迅速且準確的進行質量控制及預測成為了成飛目前在質量方面亟待解決的問題。作為一個航空類企業(yè),,成飛最大的生產(chǎn)特點就是多品種小批量,。基于多品種小批量的生產(chǎn)方式,,傳統(tǒng)的質量控制方法在生產(chǎn)過程中出現(xiàn)了種種的不適應性,,時常出現(xiàn)虛報及漏報的情況,造成生產(chǎn)過程無謂的停工檢查及返工,,從而大大提高了質量成本。
隨著數(shù)字化與信息化建設的推進,,公司各個生產(chǎn)經(jīng)營系統(tǒng)積累了豐富的原始數(shù)據(jù),,為進行大數(shù)據(jù)分析奠定了基礎。如何從這些數(shù)據(jù)中分析挖掘出關鍵質量信息,,用于提高產(chǎn)品質量及成品率,,是質量控制的重點方向。
進行基于大數(shù)據(jù)的飛機質量管控關鍵技術研究與應用是成飛的企業(yè)信息化發(fā)展到信息綜合利用階段的必然需求,。
2 飛機制造質量形成過程分析
按照過程管理的模式進行劃分,,飛機制造質量的形成過程包括工藝指令下達、生產(chǎn)指令下達,、物料配套,、現(xiàn)場執(zhí)行、質量記錄五個階段,,最終形成單機質量檔案,,如圖1所示。
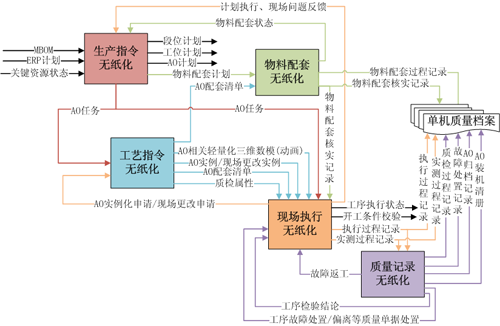
圖1 飛機制造技術架構-質量數(shù)據(jù)集成
在工藝指令下達階段,,裝配指令(ASSEMBLY ORDER,即AO)作為裝配生產(chǎn)的制造依據(jù),,是非常關鍵的工藝技術文件,以AO無紙化為突破點來實現(xiàn)工藝技術文件的無紙化,,重點突破AO實例化及基于實例的工藝現(xiàn)場更改無紙化技術難點[2],,AO的實例化依據(jù)MBOM結構及AO文檔的技術狀態(tài)、有效性和版本管理來實現(xiàn),,為每個架次的AO生成一個獨立的實例,,物流配套信息、執(zhí)行過程信息,、質量數(shù)據(jù)的采集都以獨立的AO實例為對象進行記錄,,為建立全數(shù)字化的單機質量檔案提供數(shù)據(jù)支撐。三維輕量化數(shù)模及裝配仿真動畫作為裝配制造的重要部分,將在AO實例化時一并實例化,,在制造執(zhí)行現(xiàn)場呈現(xiàn)給執(zhí)行工人進行交互使用,,以可視化方式指導工人進行裝配操作。AO實例的現(xiàn)場更改則是基于獨立的AO實例進行的工藝設計更改,,其作用范圍限定于AO實例的獨立架次有效性范圍內(nèi),。AO在執(zhí)行過程中,在更改流程驅動下可進行多次現(xiàn)場更改,,每次更改將實時反饋到MES系統(tǒng)中,,現(xiàn)場以最新版AO實例執(zhí)行,確?,F(xiàn)場使用的AO有效性,。
在生產(chǎn)指令下達階段,要解決生產(chǎn)指令生成,、發(fā)布和傳遞無紙化,。AO計劃下達時將實時關聯(lián)ERP庫房管理模塊的AO物料配套保障情況決定是否達到下達狀態(tài),同時關聯(lián)PDM判定AO文檔是否發(fā)布并具備架次有效性,。滿足物料配套條件和AO發(fā)布有效的AO計劃才能下達,,并成為工段的作業(yè)計劃。工段將作業(yè)計劃分派給操作者或操作小組,,工人接收作業(yè)任務進行現(xiàn)場執(zhí)行,。通過計劃的逐層分解及與物料配套、AO有效性的關聯(lián)達到對生產(chǎn)的有效管控,。
物料配套階段保障裝配生產(chǎn)計劃順利執(zhí)行的關鍵,,物料按計劃節(jié)點及時配套才能保障生產(chǎn)的順利執(zhí)行。物料配套無紙化,,從MES系統(tǒng)由AO的物料配套計劃驅動,,通過ERP庫房管理模塊進行物料配套、物料配送,,在生產(chǎn)現(xiàn)場由MES系統(tǒng)進行現(xiàn)場物料接收,、現(xiàn)場物料核實。在現(xiàn)場物料接收和核實環(huán)節(jié),,由工人,、檢驗分別在無紙化AO文檔上記錄和核實物料的關鍵質量信息,包括物料圖號,、配套架次,、質量編號、數(shù)量等,。AO的配套物料信息和核實質量信息將作為AO開工條件檢查的條件之一進行校驗,。在物料配交接環(huán)節(jié)使用二維碼技術,,進一步校對實物和信息流的一致性,確保物料實際配套的準確性,。
裝配現(xiàn)場執(zhí)行階段依據(jù)無紙化生產(chǎn)指令,、無紙化工藝技術文件、無紙化物料配套信息?,F(xiàn)場執(zhí)行面向操作層的操作者,、檢驗員。現(xiàn)場執(zhí)行的無紙化包括:(1)AO實例化,,由MES向CAPP提出AO實例化申請并獲取AO實例,;(2)工序開工條件核實,系統(tǒng)將自動進行工序開工條件檢查,,具備開工條件的AO允許進行工序的執(zhí)行,。(3) 工序的開完工信息采集,工人依據(jù)無紙化的工序說明書進行裝配操作,,并采集工序的開工,、完工信息,涉及實測記錄的工序填寫相應記錄,。(4)現(xiàn)場可視化展示,裝配現(xiàn)場執(zhí)行無紙化以裝配現(xiàn)場可視化為基礎,,在裝配現(xiàn)場展示AO級,、工序級的三維輕量化數(shù)模以及基于三維輕量化數(shù)模的裝配仿真,指導工人操作,,是現(xiàn)場工藝指導的重要輔助手段,。(5)AO無紙化現(xiàn)場更改,通過對單架次應用的有效的AO實例更改,,由一系列流程控制保障工藝現(xiàn)場更改的嚴謹性和現(xiàn)場執(zhí)行的可行性,。(6)工序質檢及故障處置,對工序的質檢及故障處置進行管控,,按照質量程序文件要求自動進行工序開工約束控制,,避免跨越工藝流程操作問題。(7)現(xiàn)場問題管理,,處理現(xiàn)場執(zhí)行過程中的問題,,通過流程協(xié)同職能部門處理(8) 計劃執(zhí)行反饋,工序執(zhí)行完成,,將完工信息自下而上反饋至AO層,、工位層、段位層,,形成執(zhí)行計劃的管理閉環(huán),。在現(xiàn)場執(zhí)行過程中通過流程驅動和技術手段,,提高生產(chǎn)管控的自動化和敏捷性。
質量記錄階段飛機裝配制對質量控制的規(guī)范性,、完整性,,準確性、可追溯性都有極為嚴格的要求,,因此,,在無紙化裝配制造中,AO質量文件的無紙化歸檔尤為重要,。AO歸檔的質量記錄包括:(1)AO裝配清冊,,記錄飛機裝配的物料信息、質量信息,、核實信息,,在從物料的配送到完工核實的流程中記錄(2)設檢工序的檢驗信息,記錄工序檢驗的結論,,由現(xiàn)場工序檢驗時記錄完成,。(3)現(xiàn)場實測記錄表,記錄制造過程中需實時測量的技術指標數(shù)據(jù),,由工人,、檢驗等人員錄入、簽字記錄完成,。(4)工序故障及質量單據(jù)信息,,由工序檢驗發(fā)起相關不合格品通知單、不合格品審理單等質量單據(jù)審理信息及處置結論(5)AO更改記錄,,記錄AO的歷史更改記錄及現(xiàn)場更改的內(nèi)容,、簽審信息等。(6)AO歸檔信息,,由系統(tǒng)自動進行AO歸檔條件的綜合判定,,當AO執(zhí)行完成并滿足歸檔條件時,允許進行AO電子歸檔,。AO的質量歸檔文件與質量證明文件,、質量報告等其他質量信息一并匯總,以BOM為牽引形成單機質量檔案,。
3 基于大數(shù)據(jù)的質量管控
以全面提升成飛公司飛機制造質量管控水平為宗旨,,開展了基于規(guī)則大數(shù)據(jù)分析的質量管控技術研究。研究復雜產(chǎn)品質量管控技術在航空制造業(yè)的應用情況,,分析并梳理成飛公司質量管理的現(xiàn)狀,。以“精準定位”、“反哺生產(chǎn)”為管控目標,,構建基于大數(shù)據(jù)分析的質量管控體系,。研究基于MaHout數(shù)據(jù)挖掘技術的應用模式,,實現(xiàn)流程依據(jù)挖掘出的關鍵信息自動控制質量管理的集成應用?;陲w機產(chǎn)品制造過程質量檢驗與控制業(yè)務,,研究基于統(tǒng)計過程控制方案及穩(wěn)定性預警技術,實現(xiàn)產(chǎn)品制造過程質量管控模式從事后被動檢驗轉變?yōu)?/span>事前主動預防,,從而達到提高產(chǎn)品質量及成品率,。建立質量管控平臺,開發(fā)完成生產(chǎn)計劃執(zhí)行情況數(shù)據(jù)分析,、物料配套數(shù)據(jù)分析,、現(xiàn)場執(zhí)行數(shù)據(jù)分析、檢驗數(shù)據(jù)分析,,與PDM/CAPP/ERP等系統(tǒng)的集成,,實現(xiàn)生產(chǎn)質量的全過程管控。梳理零件,、裝配生產(chǎn)制造的質量控制業(yè)務流程,,建立業(yè)務流程對應的質量指標數(shù)據(jù),實現(xiàn)業(yè)務流程與指標數(shù)據(jù)采集的協(xié)同管控,。研究單機質量交付狀態(tài)清理的業(yè)務流程和大數(shù)據(jù)分析相關技術,,實現(xiàn)單機質量交付狀態(tài)的快速清理。建立QBOM的目錄體系結構,,通過數(shù)據(jù)分類和整理,,實現(xiàn)QBOM目錄結構的單機質量檔案管理。
2.1 總體架構
基于大數(shù)據(jù)的質量管控總體技術架構如圖2所示,,整體分為大數(shù)據(jù)技術集成環(huán)境、大數(shù)據(jù)應用開發(fā)工具和大數(shù)據(jù)業(yè)務應用三個部分,。
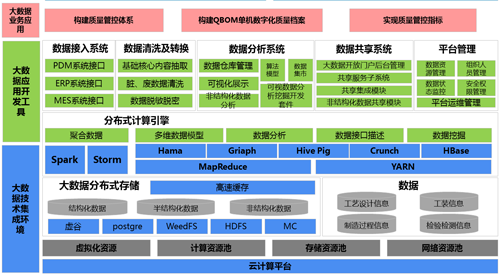
圖2 系統(tǒng)架構圖
大數(shù)據(jù)技術集成環(huán)境是進行大數(shù)據(jù)分析的技術和平臺基礎,。搭建基于云計算和HDFS的虛擬化資源池、存儲資源池,、網(wǎng)絡資源池以及基于Spark的計算資源池,,形成能夠處理各類數(shù)據(jù)的大數(shù)據(jù)分析環(huán)境,主要處理的數(shù)據(jù)包括結構化數(shù)據(jù),、非結構化數(shù)據(jù)及半結構化數(shù)據(jù)等按數(shù)據(jù)結構劃分的數(shù)據(jù)和工藝設計數(shù)據(jù),、工裝數(shù)據(jù)、制造過程數(shù)據(jù),、檢驗數(shù)據(jù)等按業(yè)務劃分的數(shù)據(jù),。大數(shù)據(jù)應用開發(fā)平臺工具是進行質量管控的中間層,主要包含分布式計算引擎,、業(yè)務數(shù)據(jù)接入系統(tǒng),、數(shù)據(jù)清洗轉換過程,、數(shù)據(jù)分析系統(tǒng)和數(shù)據(jù)共享系統(tǒng)。大數(shù)據(jù)業(yè)務應用層是質量管控的業(yè)務分析層,,主要包括構建質量管控體系,、構建QBOM單機數(shù)字化質量檔案、實現(xiàn)質量管控指標等內(nèi)容,。
2.2 主要內(nèi)容
基于大數(shù)據(jù)的飛機質量管控的復雜性首先體現(xiàn)在實物相關的質量信息數(shù)據(jù)分類多,、數(shù)據(jù)信息大、質量數(shù)據(jù)流程復雜等特點,,本次技術研究主要以業(yè)務流程為導向,,建立了質量信息采集控制管理流程,從開始零件原材料下料到零件投產(chǎn),,后續(xù)制造質量數(shù)據(jù)采集,、到零件交付歸檔,以及在實際制造過程中的實測記錄值等,,都有嚴格的流程控制,,系統(tǒng)梳理了每一個控制流程節(jié)點應該采集的數(shù)據(jù)值信息,規(guī)范了質量數(shù)據(jù)信息采集的流程和數(shù)據(jù)的規(guī)范性,,建立了飛機制造過程質量管理體系,。
從裝配環(huán)節(jié)來說,同樣梳理相應的質量管理流程和數(shù)據(jù)采集數(shù)據(jù)信息,,同時裝配主要質量很大程度上也取決于配套零件,、成品、標件等子件信息數(shù)據(jù),,系統(tǒng)通過配套管理和二次配套管理有效解決裝機信息管理問題,,同時與質量單據(jù)信息系統(tǒng)集成,包括質量單據(jù)系統(tǒng)與設計集成,,實現(xiàn)廠所協(xié)同管控的質量管控體系,,不僅實現(xiàn)了實際AO質量 信息管理,同時AO對應裝機子件的質量信息一起通過大數(shù)據(jù)技術建立實時分析關聯(lián),,從而實現(xiàn)AO質量體系建立,。
建立以QBOM為目標的單機質量檔案?;诖髷?shù)據(jù)的飛機質量管控的主要目標是實現(xiàn)以QBOM為目標的單架次產(chǎn)品質量檔案的輸出管理,,系統(tǒng)從FO歸檔、AO歸檔,、交付狀態(tài)清理三個環(huán)節(jié)分別建立零件FO檔案,、裝配AO檔案、單架次產(chǎn)品質量信息檔案,。FO歸檔實現(xiàn)了零件生產(chǎn)制造過程所有質量信息的無紙化的歸檔,。AO 歸檔實現(xiàn)了裝配生產(chǎn)制造過程所有質量信息的無紙化的歸檔,。單機質量檔案主要通過系統(tǒng)設計的合格證管理、條碼技術使用,、加上應用系統(tǒng)圖號,、質量編號、件號等信息,,建立了零件與裝配的松耦合的關系,,同時通過系統(tǒng)設計和相關技術的使用,系統(tǒng)通過對合有效管理,,有效解決裝配環(huán)節(jié)對合對單機質量的影響,,從而實現(xiàn)了生產(chǎn)管理與質量管理的協(xié)同,最終實現(xiàn)以QBOM為目標的單架次產(chǎn)品質量檔案歸檔管理,。
在國內(nèi)首創(chuàng)了跨廠所異地協(xié)同RFV(不一致處理單)全過程數(shù)字化,、流程化處理機制,解決了制造過程中不一致處置和裝配執(zhí)行集成管控的應用難題,,實現(xiàn)了跨平臺異地產(chǎn)品裝配制造執(zhí)行過程質量信息和過程的閉環(huán)管理,。基于三維數(shù)模工藝指令構建了集生產(chǎn)執(zhí)行管控,、工藝變更控制,、物流配送、質量追溯于一體的管控模型,,基于QBOM建立了單機數(shù)字化質量檔案,,實現(xiàn)了裝配制造現(xiàn)場無紙化和三維可視化。
2.3 關鍵技術
(1)基于分類算法的工藝改進管理
本項目通過對保留原因分類和故障原因關聯(lián)分析,,找出了影響工藝設計的關鍵因素,,通過改進措施,降低了此因素的發(fā)生概率,,從而提高了工藝設計成功率,。
(2)實現(xiàn)多樣化數(shù)據(jù)采集及分析,將分散數(shù)據(jù)集中管理,,建立企業(yè)級質量數(shù)據(jù)庫
通過本項目將ERP、PDM,、RFV等多個生產(chǎn)系統(tǒng)中質量相關的結構化數(shù)據(jù),,以及這些系統(tǒng)的日志文件,圖形文件等非結構化數(shù)據(jù)進行統(tǒng)一采集和管理,,建立了企業(yè)級質量數(shù)據(jù)庫,。
(3) 高效的數(shù)據(jù)分析功能
本項目通過使用Spark數(shù)據(jù)分析工具,能夠快速的找出影響某一指標的關鍵因素,,實現(xiàn)高效分析,。
(4)基于統(tǒng)計過程控制(SPC)的質量管控技術
結合飛機產(chǎn)品制造過程質量管控業(yè)務實際,,對基于統(tǒng)計過程控制(SPC)及穩(wěn)定性預警的質量管控技術進行研究,為制造過程關鍵工序提供質量過程統(tǒng)計,、分析,、預警、診斷全面過程管理的決策方案,,及時發(fā)現(xiàn)關鍵工序生產(chǎn)過程的變異,,消除異常波動,使生產(chǎn)制造處于穩(wěn)定狀態(tài),。
統(tǒng)計過程控制即應用統(tǒng)計學相關理論及技術對過程中的各個階段應用控制圖進行監(jiān)控,,對異常的點進行診斷分析,從而達到保證和改進質量的目的,。本次研究基于統(tǒng)計過程控制的質量管控方案主要包括以下內(nèi)容:
? 質量信息管理
實現(xiàn)生產(chǎn)過程關鍵工序的質量信息管理,,提供及時的、基于分析的報告和警示,,滿足管理生產(chǎn),、審計和工業(yè)標準化質量報告的要求。
? 統(tǒng)計過程控制與分析
實現(xiàn)生產(chǎn)過程關鍵工序的過程管理,、持續(xù)過程改進,、提供詳盡全面的一元及多元小批量的SPC分析,并對過程異常進行報警,。統(tǒng)計過程控制(SPC)技術使用統(tǒng)計控制圖對過程績效及其波動因素進行監(jiān)控和分析,。通過建立統(tǒng)計控制圖,可以實時地對生產(chǎn)過程的各種輸出特性進行統(tǒng)計監(jiān)控與分析,,以便及時發(fā)現(xiàn)導致質量特性發(fā)生變化的異常原因,,并及時剔除或減少異常原因,使質量特性的波動處于統(tǒng)計穩(wěn)定狀態(tài),。統(tǒng)計過程控制及分析模塊基于質量特性的相關性分析,、過程能力分析等關鍵技術,提供用于常規(guī)過程管理,、持續(xù)過程改進,、針對不同特點和類型的SPC控制圖(包括一元常規(guī)控制圖、小批量計量值控制圖,、多元計量值控制圖),,并提供報警系統(tǒng)(通過判斷控制限、警示限及違反模式進行監(jiān)控過程的報警),。
? 統(tǒng)計過程診斷
通過對工序質量影響因素的分析,,實現(xiàn)對過程異常發(fā)生原因和地點的診斷,為迅速解決質量問題提供方向和目標。統(tǒng)計過程診斷(SPD)模塊根據(jù)質量指標的一元及多元性,,分別采用不同的方法,,對異常工序或對多質量指標中的異常質量指標進行定位,從而幫助操作人員及時識別,、判斷,、分析和處理異常,并對生產(chǎn)進行改進,。該模塊基于主成分分析法(PCA)來實現(xiàn)多元SPD的診斷,,其基本思路如下:尋找一組新變量(即主成分)來代替原變量,當SPC控制圖出現(xiàn)異常點,,就需要通過制作各主成分的單變量控制圖,,將各質量特性的對失控主成分的貢獻率進行比較分析,從而實現(xiàn)工序異常判斷,。
4 結束語
本文研究了基于大數(shù)據(jù)的飛機質量管控關鍵技術,,將現(xiàn)代信息技術、自動化技術,、先進制造技術,、現(xiàn)代測量技術相結合,綜合應用于飛機的產(chǎn)品設計,、工藝設計,、生產(chǎn)制造及檢驗檢測等生命周期管理的各個階段[3]。應用大數(shù)據(jù)平臺集成各個業(yè)務系統(tǒng)質量數(shù)據(jù),,通過產(chǎn)品模型的質量控制,、質量數(shù)據(jù)的自動采集、分析與反饋控制以及質量信息資源的共享和質量管理的協(xié)同,,建立一套以數(shù)字化,、集成化、網(wǎng)絡化,、協(xié)同化為特征,,預警和報警相結合的飛機制造質量管控框架系統(tǒng)。本技術應用于飛機生產(chǎn)過程,,取得了良好的經(jīng)濟效益和社會效益,。
參考文獻:
[1] 蒲娟,許建新,,王凱,,王成,飛機制造質量保證技術研究[J],,機械制造,,2014.
[2] 余志強,陳嵩,,孫煒,,基于MBD的三維數(shù)模在飛機制造過程中的應用[J].航空制造技術,2009(S2).
[3] 張根保,,任顯林,,李明,等.基于MES和CAPP的動態(tài)質量可追溯系統(tǒng)[J].計算機集成制造系統(tǒng),,2010(2).